We’re preparing your personalized experience
It’s almost ready...
Challenges we face together
The technological landscape is evolving rapidly and at an unprecedented pace. Companies and public organizations need to innovate, become more efficient, agile, and customer-centric while ensuring business continuity and security.
Sovereign Cloud
Sensitive data maximally secured in the cloud
Why choose Proximus NXT


Sustainability commitment
Proximus NXT stands for sustainability, diversity and responsibility.
More info Opens a new window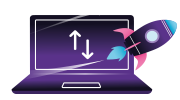
Discover our affiliates
Proximus NXT is an ecosystem of specialised affiliates and local partners. They help you manage your ICT and take advantage of new technologies in cloud, data or cyber security.
MyProximus Enterprise: discover your advantages
Not yet a MyProximus Enterprise user? Get convinced by the advantages of our platform to manage your subscriptions, your bills, and much more. Find all your Proximus services and products in one place.
Discover MyProximus Enterprise