Always count on sufficient supplies
Published on 13/07/2020 in Customer talks
An IoT solution is responsible for the level monitoring of their gas tanks. If the level in the gas tank drops below a certain threshold, Multigas schedules a new delivery. This way, the business continuity of their customers is guaranteed.

Spread across Flanders, Multigas is responsible for the supply of gas, not only in cylinders, but in tanks too. These tanks are located both in private homes and in companies, although they are generally owned by Multigas. “We have to fill those tanks regularly,” explains Ingeborg Symons, Managing Director at Multigas. “Until recently, it was primarily the customer’s job to monitor the filling level of the tank.” If the gas supply falls below a minimum threshold, the customer must notify their distributor and schedule an appointment for a gas delivery.
Do you spend a lot of time planning and calculating how much fuel or fuids you need to deliver at a certain place and time? Deliver at the right time.
Discover Smart TankDo you have any questions or would you like to launch an IoT project yourself? Then do not hesitate to contact one of our experts.
Contact usBusiness continuity
“However, in many companies, the gas supply is crucial,” Ingeborg explains and immediately lists a whole series of examples of companies where gas is an essential source of energy: coffee roasters, maize dryers, chicken breeders, asparagus growers, French fry stands, restaurants, and so on. In general, the food sector is an important Multigas customer, among others, for fueling forklift trucks. After all, food companies are not allowed to use forklifts that run on diesel. “For all these companies, the availability of gas determines the continuity of their activity.”
For this reason, until recently, a distributor visited those customers on a weekly basis to deliver gas. This was often necessary, but these frequent trips were repeatedly unnecessary too. “We had no insight into the consumption of the past week,” adds Ingeborg. “If for example the French fry stand owner had just been on a week-long vacation, he didn’t need a refill. At the same time, a company that went through a period of peak consumption would ask for the distributor to drop by earlier than planned.”
800 gas tanks
Proximus found a workable model for the sector thanks to the IoT solution for the level monitoring of gas tanks. Five other gas distributors have now joined the project in addition to Multigas. Proximus has connected eight hundred gas tanks to its IoT platform in just one year. “We are continuing to build upon this experience,” adds Francis. “After all, the principle can be applied to all kinds of tanks. We also want to offer our solution to companies that need to monitor the filling level of tanks with water, fuel oil, lubricating oil, and other liquids.”
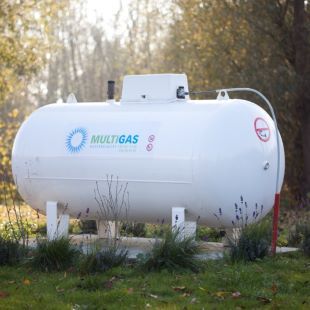
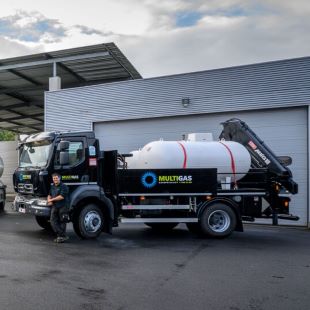
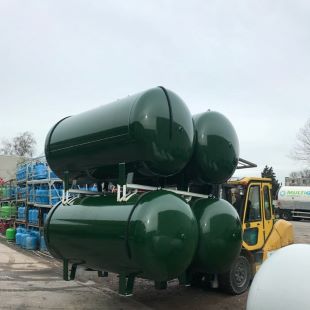
Smart meter
Proximus was familiar with these issues and set up a pilot project for Multigas. “The idea was to work out a solution based on IoT,” explains Francis Duvivier, Business Developer & Solutions Manager IoT & Data at Proximus. “We started talking to Multigas and came up with an app that would allow us to increase the operational efficiency of the company while offering a better service to the customers.” A minimum viable product was created based on the results of that interaction, a kind of basic solution, with which Proximus was able to quickly give Multigas a taste of the added value that the company could realize via IoT.
A gas tank comes with a gauge indicating the filling level as standard. Proximus decided to replace that meter with a digital one. That smart meter contains a sensor and is connected to a communication module. At fixed times – usually four times a day – the sensor reads the filling level of the gas tank. The solution transmits the encrypted measured value to Proximus’ IoT platform via the LoRa network.
There, the application converts the received data into a piece of useful information: namely, the concrete filling level of the tank. Specific actions are then linked to that value. “As from a certain filling level, the system will send a message to the distributor so that the distributor can immediately schedule a delivery,” says Francis. “If it’s very urgent, the system sends out alerts via text message, email, or an alarm on the monitoring app.”
The level monitoring via IoT ensures peace of mind. The customer no longer has to monitor the filling level of the tank personally. And yet they’ll never run out of gas.
Ingeborg Symons
Peace of mind
Thanks to the system, the distributor has a continuous overview of the status of all the tanks that it manages. That is what Multigas ultimately wanted. In the meantime, the pilot project encompasses 125 Multigas tanks. “We can now ensure that the customer always receives a new gas delivery on time,” says Ingeborg. “They no longer need to call us. They don’t have to monitor the filling level anymore and can still count on never running out of gas.”
This provides a great deal of reassurance, particularly for customers with peak consumption. “When the corn dryers are running at full speed, we read the filling volume of the tanks more than four times a day. We often have to deliver several times a day. These companies obviously cannot run out of gas at such a busy time.”
Thanks to the level monitoring, we can organize our deliveries more efficiently. We avoid a lot of unnecessary trips.
Ingeborg Symons
Gas as a Service?
Ingeborg does not want to refer to the new working method as Gas as a Service just yet. “We still need to install the tanks, there are interventions by technicians, and so on. But the level monitoring is already a step in the right direction.” Especially when Multigas also gives the available information back to the customer. “We measure daily energy consumption. It is also interesting for customers to have this information at their disposal. It is an extra service with which we distinguish ourselves in the market.”
Operational efficiency
But Multigas itself also benefits significantly from the solution. “We’re in a difficult market,” explains Ingeborg. “The government regulates fuel prices while we are on a downward trend. Gas consumption is decreasing.” And this is the context in which Multigas must work as efficiently as possible.
“Thanks to the level monitoring, we save ourselves a lot of unnecessary trips and thus do our part for the environment. If a customer is on vacation, then we can immediately see that a new delivery isn’t necessary yet. Generally speaking, we can now lower the filling level of customers’ tanks in a safe way and then fill them optimally in one go. This allows us to carry out deliveries much more efficiently.”
What perspectives can IoT offer you? Download our free IoT starter guide and discover how IoT can help your business progress.
Free IoT starter guideIngeborg Symons is Managing Director at Multigas.
1990 –1991: MBA Hartford University, Paris France/ Connecticut USA
1991 – 1997: Account Manager petrol stations - Shell Belgium nv
1997 – 2010: director at Gandagas Company nv and Gasbottling nv
2010 – Present: Managing Director at Multigas nv (before Gandagas Company nv)
Multigas supplies gas in tanks and cylinders, supplemented with the associated services. The company’s roots go back to 1959. Ingeborg Symons represents the third generation now at the helm of the company. Multigas is the result of the merger of five strong, local players, which is why Multigas grew into the largest independent supplier of propane gas in Flanders. The company has 25 employees and 50 cylinder distributors.
One
One magazine is the Proximus B2B magazine for CIOs and IT professionals in large and medium-sized organisations.